Understanding Oil Seal Engine: Importance and Applications for Diesel Engines
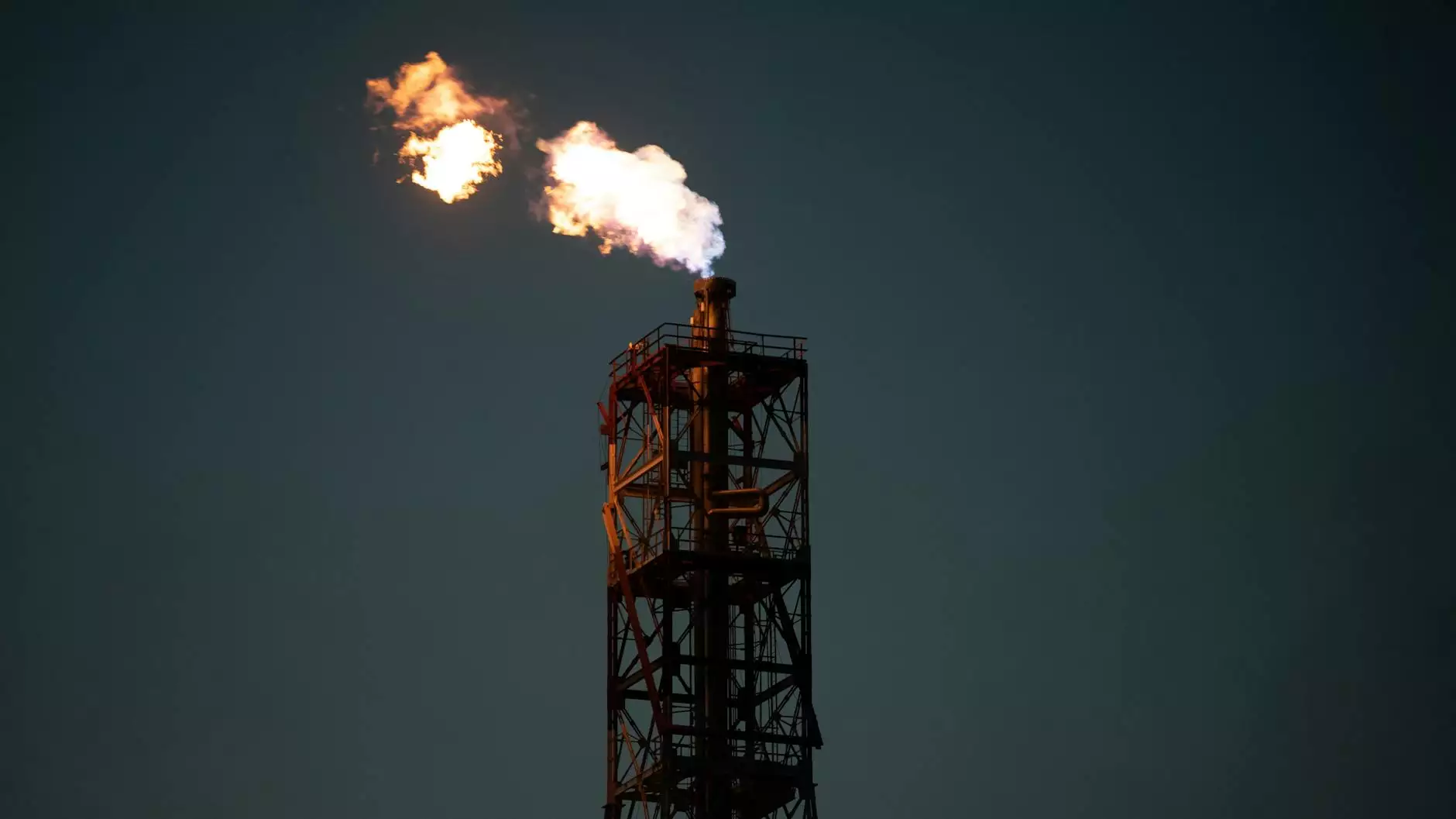
In the world of diesel engines, oil seals play a pivotal role in ensuring the smooth operation and longevity of machinery. The term oil seal engine encapsulates a vital component that not only prevents lubricant leakage but also protects internal engine parts from contaminants. This article delves deep into the intricacies of oil seals, their types, functionalities, and best practices for choosing the right one for your diesel engine, especially for businesses and professionals in the Diesel Engine Parts and Spare Parts Suppliers sectors like client-diesel.com.
What is an Oil Seal Engine?
An oil seal engine is fundamentally a device designed to seal the openings where various engine components connect to prevent the escape of lubricating oil and the entry of dust, dirt, or moisture. It is primarily utilized in the following applications:
- Prevent Oil Leakage: This is the primary function, ensuring that the engine remains lubricated.
- Block Contaminants: Oil seals serve as barriers against debris and contaminants that can damage engine performance.
- Enhance Engine Efficiency: By maintaining proper lubrication levels, oil seals contribute to overall engine efficiency.
Types of Oil Seals Used in Diesel Engines
Understanding the different types of oil seals is crucial for anyone involved in the diesel engine parts industry. The primary types of oil seals commonly used in diesel engines include:
1. Lip Seals
Lip seals are perhaps the most common type of oil seals, characterized by a flexible lip that makes contact with the shaft or housing. They are highly effective at maintaining pressure and preventing lubricant loss.
2. Rotary Seals
Rotary seals are designed to seal rotating shafts in applications where there is high speed and temperature. They are often constructed with elastomers and are used extensively in modern diesel engines.
3. Fixed Seals
Fixed seals, or static seals, do not move with the motion of the machine components. They provide reliable sealing in non-rotating applications.
4. V-Seals
V-seals are conical seals designed to protect against contaminants while retaining lubricants. They are often found in areas where they can prevent dirt ingress.
The Functionality of Oil Seal Engines
The functionality of an oil seal engine can be broken down into several, crucial responsibilities:
- Preventing Lubricant Leakage: A well-functioning oil seal is imperative in ensuring that engine oils do not seep out, which can lead to overheating and engine failure.
- Protection from Contamination: Oil seals prevent dirt and moisture from infiltrating the engine, which is critical for maintaining optimal engine performance.
- Maintaining Pressure: Oil seals help maintain the necessary pressure within the engine components, ensuring that the lubricating oil circulates effectively.
Choosing the Right Oil Seal for Your Diesel Engine
Selecting the appropriate oil seal for your diesel engine involves understanding the operational conditions and specific requirements of your machinery. Here are crucial factors to consider:
1. Size and Fit
Ensure that the oil seal you choose matches the specifications and dimensions required for your engine. A loose or overly tight seal can lead to failures.
2. Material Composition
Different applications require oil seals made from various materials. Compressible materials like Nitrile Rubber (NBR) are commonly used for their flexibility and durability, while Fluoroelastomers (FKM) offer greater temperature resistance.
3. Environmental Considerations
Consider the operational environment of the diesel engine. Higher temperatures and exposure to chemicals can affect the seal's longevity and performance.
4. Pressure Rating
Choose an oil seal that can withstand the pressure levels within your diesel engine. This ensures that it functions effectively without compromising performance.
Applications of Oil Seal Engine in Diesel Engines
The applications of oil seal engines in diesel engines extend across various sectors:
1. Automotive Industry
In the automotive sector, oil seals are critical for passenger vehicles, trucks, and heavy-duty machinery. They ensure engine oil remains contained, thereby improving longevity and performance.
2. Agricultural Machinery
Agricultural equipment, such as tractors and combine harvesters, heavily relies on oil seals to maintain engine lubrication, aiding in effective operation during demanding tasks.
3. Construction Equipment
Construction machinery including excavators and bulldozers depend on reliable oil seals to prevent leakage and optimize engine performance, even in rugged conditions.
4. Marine Engines
Oil seals are crucial in marine diesel engines, protecting them from the harsh marine environment while ensuring efficient operation.
Common Problems Associated with Oil Seal Engines
Despite their robustness, oil seals can encounter various problems that can lead to performance issues. Here are some common concerns:
1. Wear and Tear
Over time, oil seals can become worn due to continuous exposure to heat and friction, compromising their sealing capabilities.
2. Improper Installation
If an oil seal is not installed correctly, it can lead to leaks and eventual engine failures. Thus, proper installation techniques must be employed.
3. Material Degradation
Environmental factors, such as extreme temperatures and chemical exposure, can lead to the degradation of the seal material, resulting in premature failure.
4. Misalignment Issues
Improper alignment of components can stress oil seals, causing them to fail sooner than expected.
Best Practices for Oil Seal Maintenance
To maximize the lifespan of oil seals in diesel engines, businesses and maintenance teams should adhere to the following best practices:
- Regular Inspections: Conduct periodic inspections to identify signs of wear and leakage early on.
- Correct Installation: Ensure seals are installed using the right techniques and tools, following manufacturer guidelines.
- Use Quality Products: Always choose high-quality oil seals suited for your specific application to ensure reliability.
- Monitor Operating Conditions: Stay vigilant about the operating environment and conditions to preemptively address potential issues.
The Future of Oil Seal Engine Technology
The evolution of technology continuously enhances the design and capabilities of oil seals. Innovations are focused on creating seals that can withstand more significant pressures and extreme temperatures, all while minimizing wear. Upcoming technologies may include:
- Sustainable Materials: Development of biodegradable seal materials to reduce environmental impact.
- Smart Seals: Integration of sensors in oil seals for real-time monitoring of seal condition.
- Improved Lifespan: Research into advanced materials that prolong the lifespan and performance of seals significantly.
Conclusion
In conclusion, understanding the role of the oil seal engine in diesel engines is crucial for maintaining operational efficiency and longevity. By choosing the right oil seal, adhering to best maintenance practices, and staying aware of potential issues, businesses, especially those in the Diesel Engine Parts and Spare Parts Suppliers sectors, can ensure reliable engine performance. As technology continues to evolve, the future of oil seal technology looks promising, paving the way for more efficient and safer engine operation in the years to come.